MB&F Arachnophobia
After Melchior, the friendly one-foot tall robot buddy clock created in collaboration with L’Epée 1839, and the Star Wars inspired MusicMachine 3 made with JMC Lutherie, MB&F continues to celebrate its 10th anniversary in a highly creative manner by unveiling another original clock, called Arachnophobia.
Just as Melchior, Arachnophobia, the spider shaped clock is the result of collaboration between MB&F and the high-end Swiss clockmaker L’Epée 1839.
Arachnophobia was inspired by a giant spider sculpture called Maman that Büsser had seen in both Geneva and Doha. Maman (mother in French), was created by Louise Bourgeois (1911 – 2010) in bronze, stainless steel, and marble. Measuring 9.27 x 8.91 x 10.24 metres (more than 30 x 33 feet), the monumental sculpture has been installed in a variety of locations around the world.
Büsser developed the highly unusual concept with L’Epée, selecting a high-end L’Epée clock movement and re-imagining it as the mechanical head and torso of a spider. The body is outfitted with a black dome with white numerals depicting the hours and minutes. The araneae’s self-sufficiency is to be admired, for the finely-finished, highly-visible movement boasts a power reserve of eight days.
At either end of Arachnophobia’s time-displaying abdomen, important mechanical processes take place: the head houses the regulator with its oscillating balance wheel (and a set of jaws in case it gets peckish at night), while the other end contains the mainspring barrel, which powers the movement. Attached to the abdomen are eight, visually enticing legs articulated where they join the body by ball-and-socket joints. The legs can be rotated so that Arachnophobia can stand tall on a desk or splayed flat for wall mounting. A third position provides an optical treat for fans of large arachnids: the front legs can be moved forward while the six others maintain the standing position, an interesting and alarming posture that says, look out!
While Arachnophobia is not nearly as large as the sculpture that inspired it, at 405 mm in diameter with the legs fully extended, or hanging on a wall, it is certainly large enough to make a real impression. Whether that impression is positive or negative depends on how much you enjoy creepy-crawlies.
Arachnophobia comprises no fewer than 218 components, each one (except the jewels) machined and finished at L’Epée’s Swiss atelier.
Manufacturing realistic legs to faithfully replicate MB&F’s unusual design was no easy task. L’Epée had to find a solution for the legs that ensured that they would be both realistic-looking and articulated. The legs also had to conform to the standards of high watchmaking in that they could be nicely finished by hand. L’Epée came up with the novel solution of injection moulding metal to obtain the precise geometry needed. Injection moulding is a process of manufacturing components by injecting material (in this case metal) into a mould. The material is first subjected to high heat, then forced into the mould cavity. It then cools to the desired shape before being removed from the mould. While this is a very common process for shaping plastics, it is less common for shaping metals.
“When the legs come out of the injection mould, they are really rough and need a lot of attention to be as nicely finished as they are in the end,” says L’Epée CEO Arnaud Nicolas. “All of the finishing is accomplished by the hands of master finishers, who grind, satin-finish, polish, and then plate or lacquer the legs depending on the version.”
Finishing techniques used on the clock’s “body” and legs include anglage, mirror polishing, satin finishing, circular satin finishing, sand-blasting, and polishing. “The most important thing was to play with light on each one of the spider’s parts,” Arnaud Nicolas continues. “Some of the parts were sandblasted to continue the light play.”
The eight legs are connected to the clock “body” by balland-socket joints. By rotating them the legs can be made to go flat; turning them around again allows them to stand up high like the Bourgeois sculpture that inspired them.
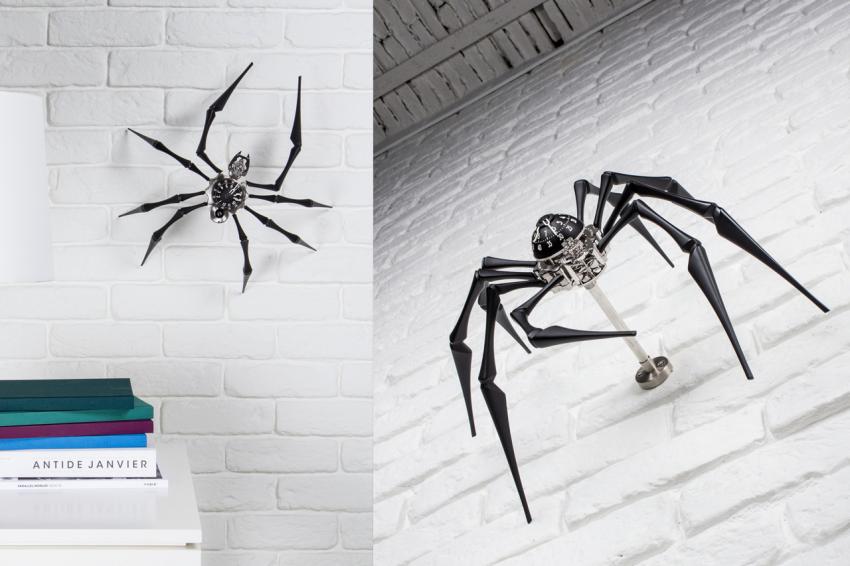
Under its belly, Arachnophobia hides an innovative system that can be used to hook it to a bracket and hang it on a wall.
To really make a statement, L’Epée has also developed a system enabling Arachnophobia to be hung on a wall. An
innovative catch underneath the movement hooks on to a stainless steel wall bracket.
The movement too features superlative fine finishing of the type generally found on the finest wristwatches, including Côtes de Genève, anglage, polishing, sand-blasting, and circular and vertical satin finishing. However, finely finishing a clock movement is far more challenging than finishing a wristwatch because of the greater surface areas of the larger components. L’Epée CEO Arnaud Nicolas explains: “It’s not simply a case of double the size of the components, double the time it takes to finish them. The complexity increases exponentially. For polishing, for example, you need to apply the same pressure as when finishing a watch movement but on a bigger surface – and any variation in that pressure is visible.”
To wind and set the time on Arachnophobia, its owner has to interact in an intimate way with the spider, by turning the underside like a key.
To further explore the fascinating world of Maximilian Büsser & Friends, head over to www.mbandf.com